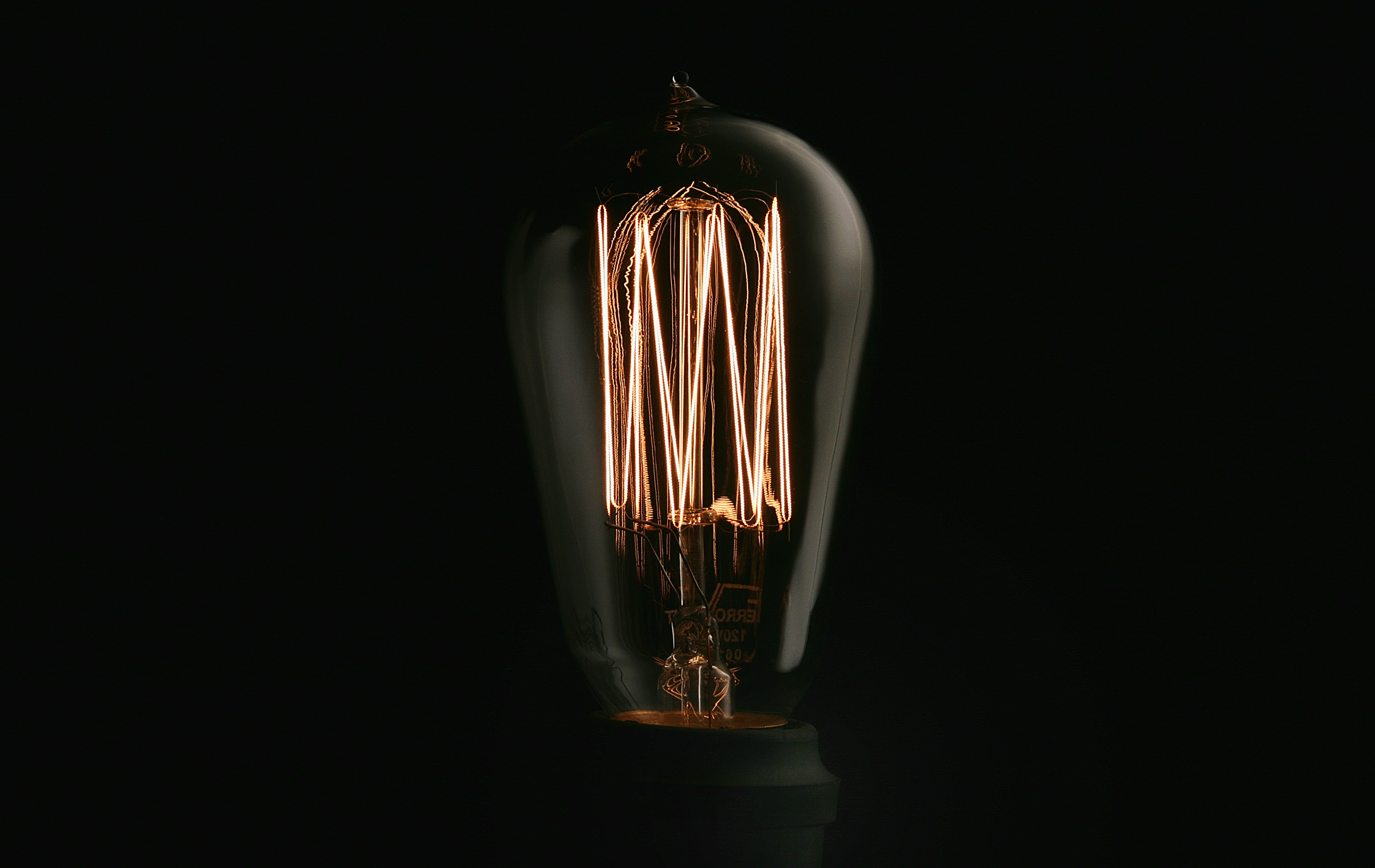
Tips for Staying Inspired: How Space Professionals Fuel Creativity and Innovation
The space industry captures our collective imagination like few others—sending probes to distant planets, launching constellations of satellites for global connectivity, even exploring the possibility of human settlements beyond Earth. From propulsion engineers and satellite architects to astrophysicists and mission control specialists, the field is a fusion of cutting-edge technology and grand ambitions. Yet, in this demanding arena, rife with rigorous testing, tight budgets, risk mitigation, and lengthy research cycles, even the most fervent space professionals can find their creative fire dwindling at times. How do people working in space—whether at government agencies, private aerospace firms, or research institutions—maintain a spark of innovation amid technical complexities, funding pressures, and enormous stakes? Below, we explore ten practical strategies to keep you inspired, inventive, and energised. Whether you’re building propulsion systems, planning satellite missions, or leading new explorations of lunar resources, these tips can help you break out of ruts, generate fresh perspectives, and push boundaries that define the future of humanity’s journey among the stars.